Tool optimization within a CNC machine is critical for efficiency and quality in machining processes.
Extended Life of Tools in CNC Machines
Improved Tool Performance in CNC Machines
Partnership in Precision: Partnering with Top Tooling Companies for Optimal Machine Integration.

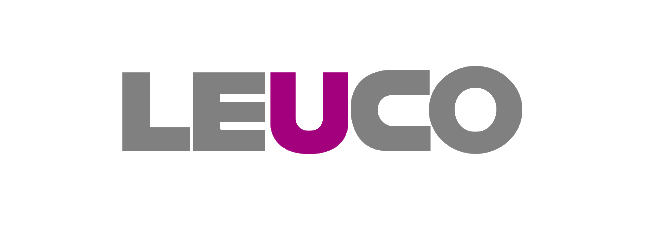
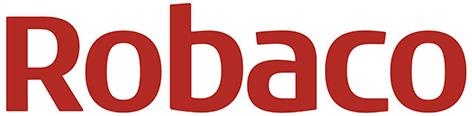
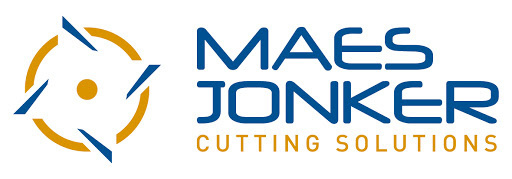
How to obtain support quickly?
Quick Support of Team Viewer download from the link below.
Then enter your name in the location provided + Description of the problem.